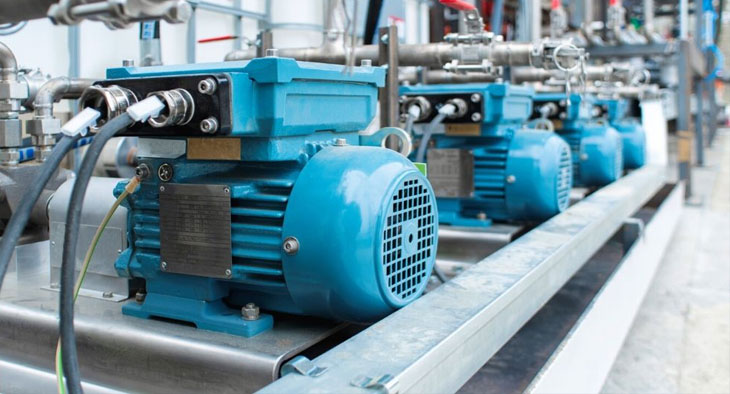
Mechanical Changes to Consider While Upgrading from IE2 to IE3 and IE3 to IE4 Industrial Motors
Team IEC
- 1
Mechanical Changes to Consider While Upgrading from IE2 to IE3 and IE3 to IE4 Industrial Motors
Upgrading industrial motors from IE2 to IE3 or IE3 to IE4 is an essential step toward achieving higher energy efficiency, reduced operational costs, and improved sustainability. However, transitioning to a high-efficiency motor isn’t as simple as replacing one motor with another. It requires careful attention to various mechanical aspects to ensure optimal performance, compatibility, and longevity.
In this blog, we’ll explore the critical mechanical changes to consider while upgrading to IE3 and IE4 motors, ensuring a smooth transition that enhances reliability and productivity while minimizing downtime.
Why Upgrade to IE3 and IE4 Motors?
Industrial motors are classified based on their International Efficiency (IE) standard ratings, where:
- IE2 (High Efficiency) Motors – Standard motors used in many industrial applications but have higher energy losses.
- IE3 (Premium Efficiency) Motors – Deliver better efficiency than IE2 motors, leading to lower power consumption and reduced heat losses.
- IE4 (Super Premium Efficiency) Motors – Provide even greater efficiency, reducing overall operational costs while enhancing reliability and performance.
Upgrading to IE3 or IE4 motors not only saves energy but also helps industries comply with global energy regulations and reduce their carbon footprint. However, these motors come with specific mechanical challenges that must be addressed before installation.
Mechanical Changes to Consider When Upgrading from IE2 to IE3
1. Frame Size and Mounting Adjustments
- IE3 motors often have a larger frame size than IE2 motors due to additional materials used to reduce energy losses.
- The mounting holes and shaft height might be different, requiring modifications to the motor base or foundation.
- Ensure proper alignment and support to avoid mechanical stress on connected equipment.
2. Shaft and Coupling Adjustments
- IE3 motors might have a longer or thicker shaft compared to IE2 motors, requiring an adjustment in couplings or pulleys.
- Verify shaft alignment to prevent misalignment issues that can lead to excessive vibration and premature bearing failure.
- Consider using flexible couplings to compensate for any slight misalignment and to absorb shocks.
3. Increased Weight Considerations
- IE3 motors are heavier due to improved lamination materials and copper windings.
- Ensure that the existing mounting structure and lifting mechanisms can support the additional weight.
- If necessary, reinforce the motor support base to prevent vibrations and structural damage.
4. Bearing Upgrades and Lubrication Adjustments
- Higher efficiency motors operate with lower energy losses, which may change the operating temperature and load on bearings.
- Some IE3 motors come with different bearing types (e.g., sealed-for-life bearings) that may require fewer lubrication intervals.
- If using standard bearings, switch to high-quality lubricants that support higher speeds and lower friction.
5. Cooling System Modifications
- IE3 motors generate less heat, but their fan design may differ from IE2 motors.
- Some applications may require adjustments in airflow management to avoid localized overheating of nearby components.
- If the new motor runs hotter than expected, consider external cooling solutions, such as forced ventilation systems.
Mechanical Changes to Consider When Upgrading from IE3 to IE4
Upgrading from IE3 to IE4 motors presents additional challenges due to even more advanced efficiency improvements. Here’s what to look out for:
1. Compact Yet Heavier Design Considerations
- IE4 motors are generally more compact than IE3 motors but contain denser materials, making them heavier.
- Verify that the mounting structure is strong enough to support the additional weight.
- If required, use reinforced brackets or additional support plates to maintain mechanical stability.
2. Permanent Magnet (PM) Motor Challenges
- Many IE4 motors use permanent magnet (PM) technology instead of induction designs, requiring special attention:
- Shaft alignment is more critical as PM motors often have higher starting torques.
- Back EMF (Electromotive Force) issues must be considered, requiring compatible drives.
- Coupling mechanisms may need extra torque absorption capacity to prevent mechanical failures.
3. Bearing and Shaft Adjustments for High-Speed Operation
- IE4 motors often have higher rotational speeds, which can lead to:
- Increased bearing stress, requiring high-speed-compatible bearings.
- More stringent shaft balancing requirements to avoid vibrations.
- Potential modifications in gearbox selection if used in a transmission system.
4. Noise and Vibration Dampening
- While IE4 motors reduce electrical losses, they might introduce new vibration frequencies due to different electromagnetic properties.
- Use vibration dampeners or advanced mounting pads to minimize noise levels.
- Consider real-time vibration monitoring to detect anomalies early.
5. Cooling System Reassessments
- IE4 motors often use different cooling methods than IE3 motors, such as advanced airflow designs or liquid cooling in some cases.
- Ensure proper ventilation and cooling ducts to accommodate the new design.
- If the motor operates in a harsh environment, check for additional cooling enclosures to prevent overheating.
Best Practices for a Smooth Upgrade
To ensure a seamless transition from IE2 to IE3 or IE3 to IE4, follow these best practices:
✅ Conduct a Mechanical Audit: Assess existing mechanical systems before installing the new motor to identify potential challenges.
✅ Use Laser Alignment Tools: Proper shaft alignment prevents premature wear on bearings and couplings.
✅ Reinforce Foundations if Necessary: If the motor is heavier, strengthen the base to avoid long-term damage.
✅ Monitor Vibration and Noise Levels: Use real-time monitoring tools to detect mechanical issues early.
✅ Work With Experts: Consult with motor manufacturers and mechanical engineers to ensure compatibility with existing systems.
✅ Update Documentation: Keep records of all mechanical changes, including alignment reports and maintenance schedules, for future reference.
Conclusion
Upgrading from IE2 to IE3 and IE3 to IE4 motors is a crucial step toward improving industrial efficiency and sustainability. However, mechanical modifications are essential to ensure seamless integration, prevent failures, and maximize the benefits of high-efficiency motors.
By addressing frame size, mounting, shaft alignment, cooling, vibration, and bearing adjustments, industries can enhance the longevity, reliability, and performance of their new motors while optimizing energy savings.
🔹 Are you planning an industrial motor upgrade? Ensure that your mechanical infrastructure is ready for the transition to achieve maximum efficiency and reliability! 🚀
best