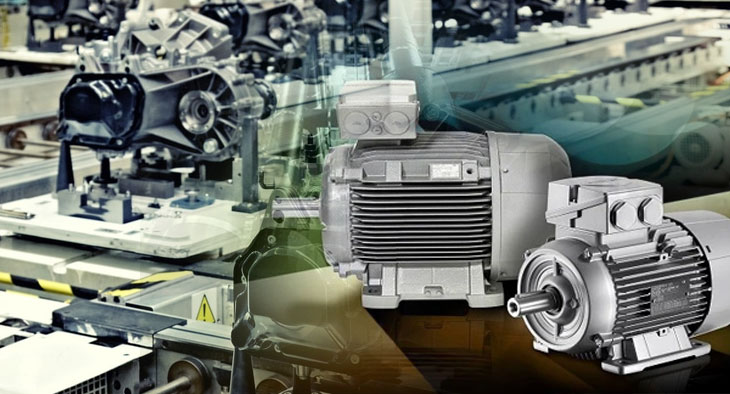
Role of Electric Motors in the Machine Tools Industry
Team IEC
- 1
Role of Electric Motors in the Machine Tools Industry
🏁 1. Introduction
Electric motors in machine tools are not just components; they are performance drivers. Whether it’s a CNC lathe or a grinding machine, motors dictate the efficiency, accuracy, and throughput of operations. For Indian manufacturers facing global competition, using the right motor is essential to stay ahead.
⚙️ 2. Types of Electric Motors in Machine Tools
Motor Type | Functionality | Control | Applications |
---|---|---|---|
AC Induction Motors | Simple, rugged, cost-effective | VFD (Variable Frequency Drive) | Conveyors, basic spindles |
Brushless DC (BLDC) | High speed, low maintenance | PWM Drives | High-speed spindles, CNCs |
Servo Motors | Precise position & speed control | Encoder/Resolver | Axis drives in CNC machines |
Stepper Motors | Discrete steps, open loop | Step control | Light-duty positioning systems |
Synchronous Motors | Constant speed | VFD + Position feedback | Grinding machines, heavy-duty spindles |
🇮🇳 3. Indian Machine Tools Industry: Market Insights
- Market Size (2024): Approx. ₹25,000 Cr
- Growth Rate: CAGR of 9% (2024–2030)
- Key Drivers:
- Government schemes like PLI, SAMARTH Udyog
- Automotive & aerospace sector expansion
- MSME digitalization push
📊 India is poised to become one of the top 5 global manufacturing hubs by 2030.
🛠️ 4. Applications of Electric Motors in Machine Tools
🔹 Lathes
- Spindle Drive: AC or BLDC motors for variable speed control
- Feed Drive: Servo or stepper for axis movement
🔹 Milling Machines
- Spindle Motors: BLDC or synchronous for high-speed operations
- Axis Motors: Servo motors for X/Y/Z precision
🔹 Grinding Machines
- Precision Spindles: Synchronous motors for minimal vibration
- Coolant Pumps: Small induction motors
🔹 Drilling & Boring Machines
- Spindle Drive: Induction motors
- Feed Mechanism: Stepper motors
📐 5. Key Performance Metrics of Electric Motors
Metric | Importance in Machine Tools |
---|---|
Power (kW/HP) | Determines cutting capabilities and material throughput |
Torque | Affects load handling during roughing or finishing |
Speed Range (RPM) | Impacts quality of surface finish and operation cycle time |
Acceleration/Braking | Reduces idle time between operations |
Thermal Load | Affects motor durability and performance under load |
Example: A 5 kW BLDC motor running at 12,000 RPM is ideal for fine finishing, while a 10 kW induction motor is better for heavy-duty roughing.
♻️ 6. Energy Efficiency and IE Standards
IE Class | Efficiency (%) | Ideal For |
---|---|---|
IE1 | < 85% | Basic machinery with intermittent duty |
IE2 | 85–89% | Mid-range usage in job shops |
IE3 | 89–92% | Continuous-duty, high-output machinery |
IE4 | > 92% | Premium, energy-sensitive applications |
⚡ Cost Savings: Replacing IE1 with IE3 motors in a 15 kW spindle can save up to ₹20,000/year in energy costs.
🔧 7. Advanced Motor Technologies
✅ Servo & Direct Drive Motors
- High torque at zero speed
- Ideal for CNC tables, pick-and-place, 5-axis machining
✅ Smart Motors (IoT Enabled)
- Sensors for temperature, vibration, current
- Integrated with dashboards for predictive maintenance
✅ Rare Earth Magnet Motors
- Neodymium-based for high performance in compact sizes
🧮 8. Motor Selection Criteria for Machine Tools
Factor | Considerations |
---|---|
Power Requirements | Match with machine tool’s spindle/feed power needs |
Duty Cycle | Continuous vs. intermittent operation |
Speed Control | Need for variable speed (e.g., VFD, Servo Drive) |
Precision Needs | CNC axes demand higher feedback and closed-loop systems |
Environment | Dust, coolant, and temperature-resistant motors (IP55–IP67 ratings) |
Lifecycle Cost | Not just price—consider maintenance, energy use, and downtime |
🛡️ 9. Maintenance Best Practices
- Routine Checks: Alignments, wear, vibration
- Thermal Monitoring: Use IR sensors to spot hotspots
- Vibration Analysis: Prevents bearing or rotor failures
- Cleaning Protocols: Regular 5S implementation improves motor life
- Lubrication & Cooling: Ensures smooth operation under continuous load
📌 Implementing predictive maintenance can reduce unplanned downtimes by over 40%.
💰 10. Impact on Productivity & Costs
Impact Area | Electric Motor Benefit |
---|---|
Cycle Time | Faster spindle acceleration & deceleration |
Surface Finish | Improved motor control = lower surface roughness (Ra) |
Downtime | Smart motors alert before failure, minimizing disruptions |
Energy Savings | Premium motors reduce electricity bills by 10–15% |
Total Cost of Ownership | Lower maintenance + power savings = higher ROI |
✅ 11. Conclusion
Electric motors are the driving force behind India’s machine tool revolution. From conventional lathes to high-precision CNCs, motors influence productivity, product quality, and energy efficiency. With India aiming for global manufacturing leadership, choosing the right electric motors—and embracing smarter, energy-efficient technologies—is no longer optional but a strategic necessity.
Your next move?
- Audit your machine tools
- Upgrade to IE3 or smart motors
- Integrate motor analytics into your factory dashboard
- Partner with certified Indian motor manufacturers for long-term success
❓ 12. Frequently Asked Questions (FAQs)
1. Which motor is best for CNC machine tools?
Answer: Servo motors are ideal for CNC axes due to high precision and feedback control. For spindles, BLDC or synchronous motors offer high speed and efficiency.
2. How do IE3 motors benefit manufacturing units in India?
Answer: IE3 motors offer higher efficiency, reducing electricity usage and long-term operating costs. With electricity costs rising, the ROI on IE3 upgrades is fast.
3. What factors should I consider when selecting a motor for a milling machine?
Answer: Consider power, torque, duty cycle, required RPM, thermal conditions, and need for variable speed or feedback.
4. Can older machines be retrofitted with smart motors?
Answer: Yes, many IoT-enabled motors support common protocols (Modbus, Ethernet/IP), making retrofit possible for older CNCs and PLCs.
5. What’s the difference between induction and servo motors?
Answer: Induction motors are cost-effective and robust for constant-speed tasks. Servo motors offer higher precision and are used in position-sensitive applications like CNC axis control.
best