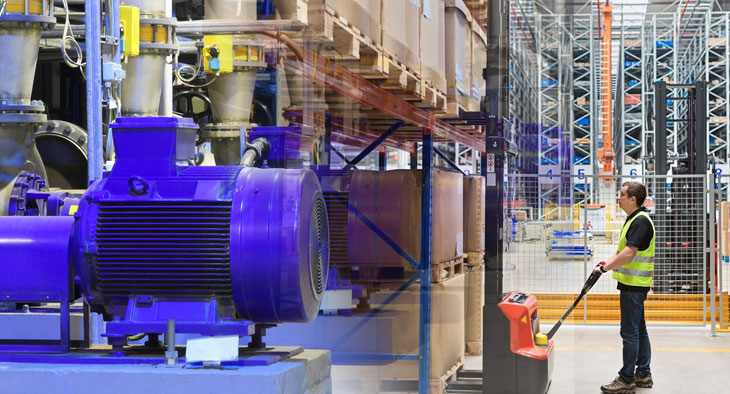
Role of Electric Motors in the Material Handling
Team IEC
- 1
Role of Electric Motors in the Material Handling
India’s logistics and manufacturing sectors are at a pivotal juncture. With the government’s emphasis on Make in India, PM Gati Shakti, and green growth, businesses must upgrade their material handling processes to remain competitive. At the heart of this transformation lie electric motors—providing the torque, precision, and energy efficiency that modern warehouses, factories, and port terminals demand.
In this article, we delve into the role of electric motors in material handling, exploring their types, applications, benefits, and best practices tailored to the Indian context. Whether you’re an operations manager at a Pune-based auto parts plant or a logistics coordinator in Chennai’s bustling port, this guide will help you make informed decisions and drive impactful results.
Understanding Material Handling
Material handling encompasses the movement, storage, protection, and control of products throughout manufacturing, warehousing, distribution, consumption, and disposal. Efficient material handling:
- Reduces labor costs by automating repetitive tasks.
- Improves safety through precise, controllable motion.
- Enhances throughput with continuous, reliable equipment.
- Supports scalability in response to fluctuating market demand.
Key equipment categories include conveyors, cranes, forklifts, automated guided vehicles (AGVs), and palletizers. In each case, electric motors transform electrical energy into mechanical motion, delivering the power and control essential for high-performance operations.
Electric Motors: The Heart of Material Handling Equipment
Nearly every piece of material handling equipment relies on electric motors for:
- Propulsion: Driving conveyors and mobile platforms.
- Lifting: Powering hoists and cranes.
- Positioning: Guiding robotic arms and palletizers.
- Control: Ensuring smooth acceleration and precise stopping.
3.1 Types of Electric Motors Used
- Three-Phase Induction Motors
- Widely used for fixed-speed applications (e.g., conveyor belts).
- Robust, low-maintenance, and cost-effective.
- Permanent Magnet (PM) Synchronous Motors
- Offer high torque density and efficiency.
- Ideal for cranes and hoists requiring rapid starts/stops.
- Brushless DC (BLDC) Motors
- Combine DC control with AC-like efficiency.
- Common in AGVs and robotic applications.
- Servo Motors
- Provide precise position, speed, and torque control.
- Used in pick‑and‑place machines and palletizers.
- Stepper Motors
- Operate open‑loop with discrete steps.
- Suited for simple applications with low torque requirements.
3.2 Comparison of Motor Types
Motor Type | Speed Control | Torque Density | Efficiency (%) | Maintenance | Typical Use Cases |
---|---|---|---|---|---|
Three‑Phase Induction | VFD‑controlled | Medium | 85–92 | Bearings, V‑belt | Conveyor belts, fan drives |
PM Synchronous | VFD‑controlled | High | 92–96 | Low (no rotor losses) | Overhead cranes, hoists |
BLDC | Electronic commutation | High | 88–94 | Low (no brushes) | AGVs, mobile robots |
Servo | Closed‑loop | Very High | 80–92 | Medium (encoders) | Robotic arms, precision positioning systems |
Stepper | Open‑loop | Low to Medium | 60–80 | Low | Simple indexing tables, small feeders |
Key Applications in India
Electric motors empower a wide array of material handling equipment in India:
- Conveyors: Assembly lines in automotive plants (e.g., Maruti Suzuki).
- Cranes & Hoists: Port terminals (e.g., JNPT in Navi Mumbai) for container handling.
- Forklifts & Pallet Trucks: Warehouses (e.g., Amazon fulfilment centres).
- Automated Guided Vehicles (AGVs): Pharma facilities in Hyderabad.
- Robotic Palletizers: FMCG bottling plants in Gujarat.
4.1 Application vs. Motor Type
Application | Preferred Motor Type | Key Requirements |
---|---|---|
Conveyor Belts | Three‑Phase Induction | Reliability, low cost |
Container Cranes | PM Synchronous + Gearbox | High torque, precise control |
Forklifts | BLDC | Battery efficiency, regenerative braking |
AGVs | BLDC + Servo | Compact size, precise navigation |
Robotic Palletizers | Servo + Induction | Accuracy, dynamic response |
Benefits of Electric Motors in Material Handling
- Energy Efficiency & Cost Savings
- VFD‑controlled motors optimize power draw, reducing electricity bills by up to 30%.
- Regenerative braking in BLDC and PM motors recovers energy during deceleration.
- Enhanced Precision & Control
- Servo and BLDC motors deliver sub-millimeter positioning, critical for high-speed packaging lines.
- Soft start/stop capabilities minimize product damage and mechanical wear.
- Reduced Maintenance & Downtime
- Brushless designs eliminate carbon brush replacements.
- Predictive maintenance algorithms (via IoT sensors) forecast bearing wear and temperature anomalies.
- Environmental Sustainability
- Lower carbon footprint aligns with India’s National Electric Mobility Mission Plan.
- Enables green warehouses—key for ESG compliance among multinational companies operating in India.
- Scalability & Flexibility
- Modular motor-driven units allow quick reconfiguration of material flow.
- Supports seasonal peaks, such as Diwali e‑commerce surges.
Technical Considerations for Motor Selection
Selecting the right motor involves balancing performance, reliability, and total cost of ownership:
- Power & Torque Requirements: Calculated from load weight and desired acceleration.
- Speed Control Range: Determines the need for VFDs or servo drives.
- Duty Cycle & Load Profile: Continuous vs. intermittent duty affects thermal design.
- Ambient Conditions & Cooling: Tropical climates demand higher IP (Ingress Protection) ratings.
- Energy Efficiency Standards: Compliance with Bureau of Energy Efficiency (BEE) star ratings.
- Size & Weight Constraints: Especially critical for mobile platforms (AGVs, forklifts).
- Integration with Automation: Compatibility with PLCs, SCADA, and IoT sensors.
- Vendor Support & Local Service: Proximity of service centres across India.
6.1 Selection Criteria & Parameters
Parameter | Description | Acceptable Range / Standard |
---|---|---|
Rated Power | Continuous output in kW | 0.5 kW to 200 kW (depending on application) |
Rated Torque | Nominal torque at rated speed (Nm) | Application‑specific (e.g., 50–500 Nm) |
Speed Range | Min‑Max speed control (RPM) | 0–3000 RPM with VFD; 0–6000 RPM for servo |
Efficiency Class | Energy performance classification | IE3 or IE4 preferred |
Ingress Protection (IP) | Resistance to dust and water | IP55 for indoor; IP66 for outdoor |
Voltage & Frequency | Supply compatibility | 415 V, 50 Hz three‑phase (standard in India) |
Duty Cycle (S) | Continuous (S1) vs. Intermittent (S2–S10) | S1 for conveyors; S3 for hoists |
Overload Capacity | Ability to handle peak torque | 150–200% of rated torque for short durations |
Trends & Innovations Shaping the Future
- IoT-Enabled Predictive Maintenance
- Vibration, temperature, and current sensors feed analytics platforms to predict faults before failure.
- Energy Recuperation Systems
- Regenerative drives in cranes and elevators send excess energy back to the grid or to battery storage.
- Digital Twin & Industry 4.0
- Virtual simulation of material handling lines for optimization, leveraging motor performance data.
- Motor Manufacturer in India
- Growth of Motor OEMs (e.g., Siemens, CG, Bharat Bijlee) for high-efficiency motors.
Conclusion
Electric motors are the unsung heroes of material handling—providing the muscle and brainpower that power India’s ambitious growth story. From Make in India factories to world‑class ports, the adoption of high‑efficiency, intelligent motor systems delivers measurable benefits: cost savings, operational resilience, and environmental stewardship. By understanding motor technologies, applying rigorous selection criteria, and embracing Industry 4.0 innovations, Indian businesses can future‑proof their material handling operations and secure a competitive edge.
FAQs
- Which type of electric motor is best for heavy‑duty cranes? Permanent Magnet (PM) synchronous motors paired with gearboxes are ideal for heavy‑duty cranes due to their high torque density, precise speed control, and regenerative braking capabilities.
- How does a VFD improve energy efficiency in conveyor systems? A Variable Frequency Drive (VFD) adjusts motor speed to match load requirements, minimizing unnecessary power draw during partial loads and enabling soft start/stop to reduce mechanical stress.
- What maintenance practices ensure long motor life in tropical climates? Regular bearing lubrication, periodic inspection of cooling fins, vibration monitoring, and ensuring the IP rating (minimum IP55) to protect against moisture and dust are critical for longevity.
- Can electric motors be retrofitted with IoT sensors? Yes—non‑intrusive current clamps, vibration sensors, and temperature probes can be retrofitted to existing motors, feeding data to predictive maintenance platforms without downtime.
- Are there government incentives for adopting high‑efficiency motors in India? Under the Bureau of Energy Efficiency’s (BEE) STAR Rating programme and Production Linked Incentive (PLI) schemes, manufacturers and end-users can avail subsidies and tax benefits for deploying IE3/IE4‑rated motors.
best